See the introduction to eBirdman Propulsion System.
The system designed to follow the modern trend of the big commercial airliners and also military jets where aircraft on-board management systems is built around the intelligent In Flight Controller with a “Glass Cockpit” display. Even so, this stage of the development should be viewed as a basic implementation of these concepts for the needs of all pilots as required in 21st century , even for recreational sport pilots.
It’s architecture is modular, made for an easy upgrades and easy replacements of the off-the-shelf components. This modular architecture means:
- Usage of standard serial interfaces most popular in today electronics
- Making program for IFC MCU well structured allowing minimal changes to accommodate hardware upgrades. Example: to change a number of the battery cells, it is enough to change 3 constants in the code, reusing the same hardware components and reusing the same IFC code communicating with BMS, etc.
- Changing the major off-the-shelf components, such as the motor and motor controller, will only require change of some constant definition in MCU code whence leaving IFC functionality almost unchanged.
The propulsion is built around the BLDC motor and it’s control: Brushless Sensored DC motor at least 15kW ( 20 HP) or more, controlled by a BLDC motor controller. Number of different motors are been tested.
Below is a Block diagram – Architecture of currently built propulsion system.
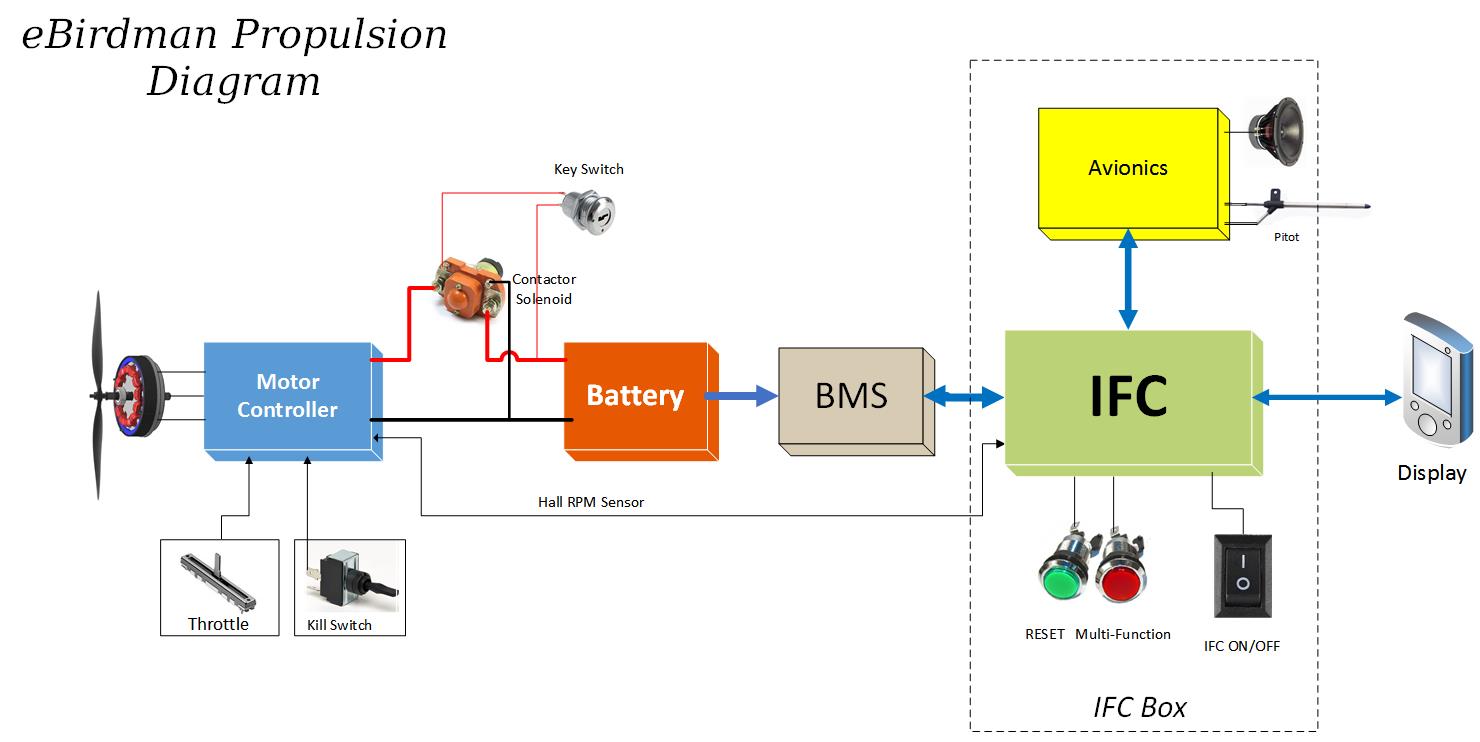
- Motor: 3-phase BLDC motor at least 15kW with 3 Hall sensors and temperature sensors.
- Motor Controller: 3-phase Hall-sensored motor controller capable up to 90v from the battery and up to 20 kW continuous motor power.
- Throttle slider potentiometer type.
- Kill switch intended to disable motor output from the controller. Notice: motor controller remains powered though.
- Key switch connects/disconnects the main battery power to the motor controller over the contactor solenoid.
- Contactor solenoid: connects/disconnects main power from the battery to the motor controller.
- Lithium Ion Polymer type Battery. Consists of two boxes connected in series (more on it read in the Battery page).
- BMS: Battery Management System consists of two modules, each connected to the respective battery box.
- IFC : In Flight Controller – similarly to all commercial airliners and military jet planes, -the main “brain” of the whole system, gathering, processing and displaying all the important data of the propulsion system, verifies if they are within working limits and generates alarms. All the flight parameters and alarms displayed on the screen of the “Glass Cockpit” Display. More on it read in IFC Operation page.
- Avionics: currently built-in module into the IFC. Avionics sensed data reported to the IFC and displayed on the IFC display. Audio for the Vario is built into the same IFC box. See more on the Avionics page .
- Display : high resolution LCD display with a touch screen – designed to be a “Glass Cockpit”, communicating with IFC module over TTY serial interface 115200 baud speed (for details see Display Overview page).